RMC takes quality as our Enterprise life,and numerous quality practices have been set up to control the quality of the castings and machining. We are consistently do whatever we can do to insure our customers receive the parts they want. Based on the recognition that rigid quality control is paramount to our customers, we take quality as our self-esteem. Well organized equipment and knowledgeable employees are the keys to our outstanding record of quality.
The strict internal standards in RMC require us to proceed strict testing and quality control procedures, beginning from the design stages all the way through final inspection. RMC is always willing to take additional steps in testing and quality control procedures so as to match or even beyond the most exacting customer requirements.
With fully-equipped materials testing laboratory and spectrometers, hardness and tensile testing machines, our colleagues could proceed the testing totally according to your unique strict requirements. We utilize NDT facility for in-house magnetic particle testing and liquid penetrant testing. Additionally, we can offer other test service with fully certified X-ray flaw testing and ultrasonic flaw testing vendors in our area from the third-party.
• ISO 9001:2015
We achieved certification to ISO-9001-2015. In this way, we standardized our production process, and made the quality stable, and also reduced the costs.
• Raw Material Inspection
Incoming raw material were kept in control strictly, because we believe raw material in good quality is the foundation of the high quality of the castings and finished products.
All the raw material like wax, water glass, aluminium, iron, steel, chromium etc are bought from the certificated sources stably. Product quality documentations and inspection reports must be provided by the supplier, and random inspection will be implemented during the materials’ arrival.
• Computer Simulation
Simulation programs tools (CAD, Solidworks, PreCast) are used to make the engineering works of casting more predictable to eliminate the defects and improve the stability.
• Chemical Composition Testing
Chemical composition analysis to the castings is required to ascertain the chemical composition of a heat of metal and alloys. Specimen will be taken and tested both pre-pouring and post-pouring to control the chemical composition within the specification, and the results must be doubled checked again by the third inspectors.
The specimens being tested also are kept well for two years for tracking using. Heat numbers can be made to keep the traceability of the steel castings. The Spectrometer and Carbon Sulfur analyzer are the main equipment for the chemical composition testing.
• Non Destructive Testing (NDT)
The non destructive testing can be processed to check the defects and inner structure of the steel castings.
- Magnetic Particle Examination
- Ultrasonic Flaw Detection
- X-ray Examination
- Penetrant Testing (PT)
• Mechanical Properties Testing
The mechanical properties testing must be done strictly by the professional equipment as in the following:
- Metallographic Microscope
- Hardness test machine
- Tension tester
- Impact strength tester
• Dimensional Inspection
Process audit will be implemented during the whole machining process of the steel castings according to the drawings and machining process card. After the steel casting parts being machined or finished the surface finish, three pieces or more pieces according to the requirements will be pick out at random, and dimensional inspection will be implemented.The inspection results are all recorded well, and represented on the paper as well as in the data-base by computer.
Our dimensional inspection can be the one or full of the following method.
- Vernier Caliper of High Precision
- 3D scanning
- Three -coordinates Measuring Machine
The following photos show how we inspect the products and control the quality for the requirements of chemical composition, mechanical properties, geometrical and dimensional tolerances. And other special tests such as thickness of surface film, inside defects testing, dynamic balancing, static balancing, air pressure testing, water pressure testing and so on.
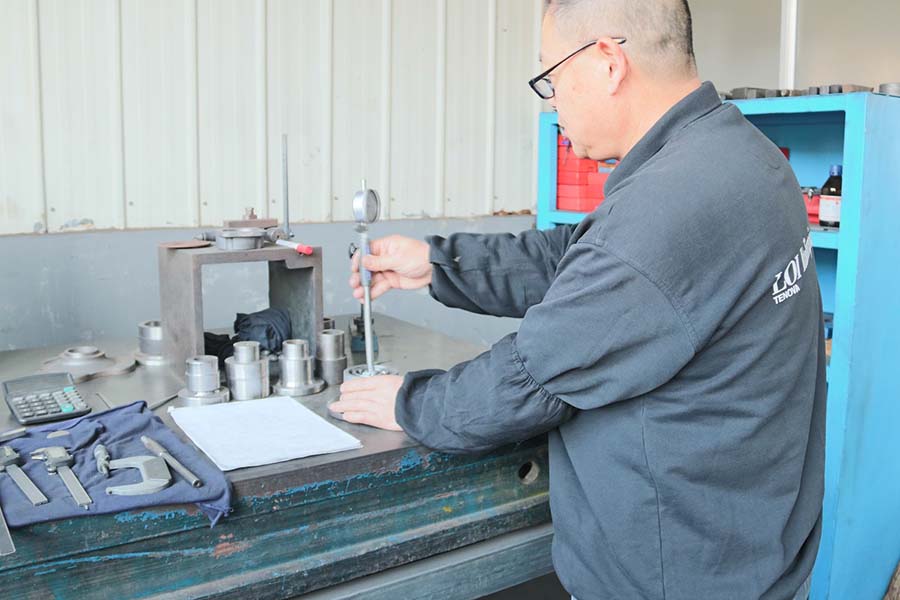
Dimension Checking
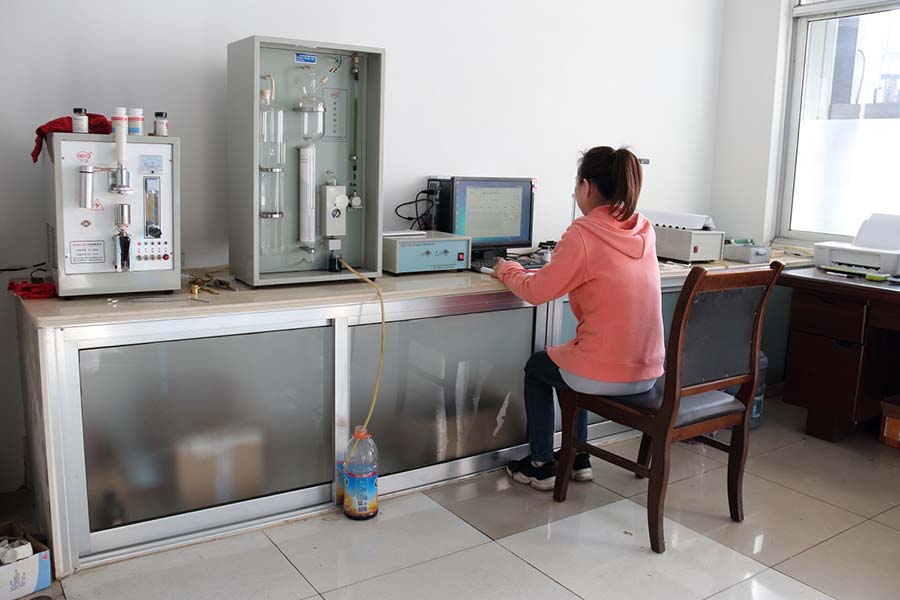
Carbon Sulfur Analyzer
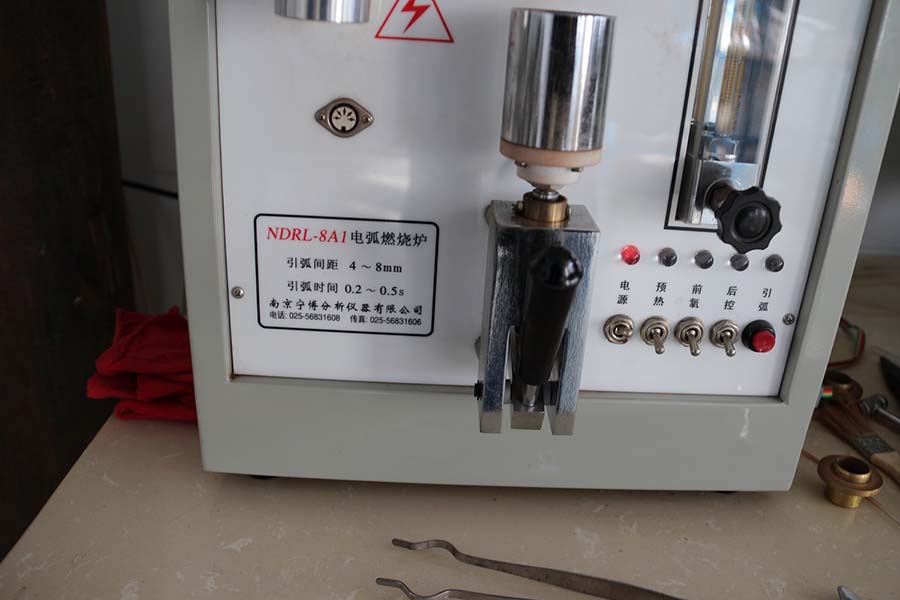
Carbon Sulfur Analyzer
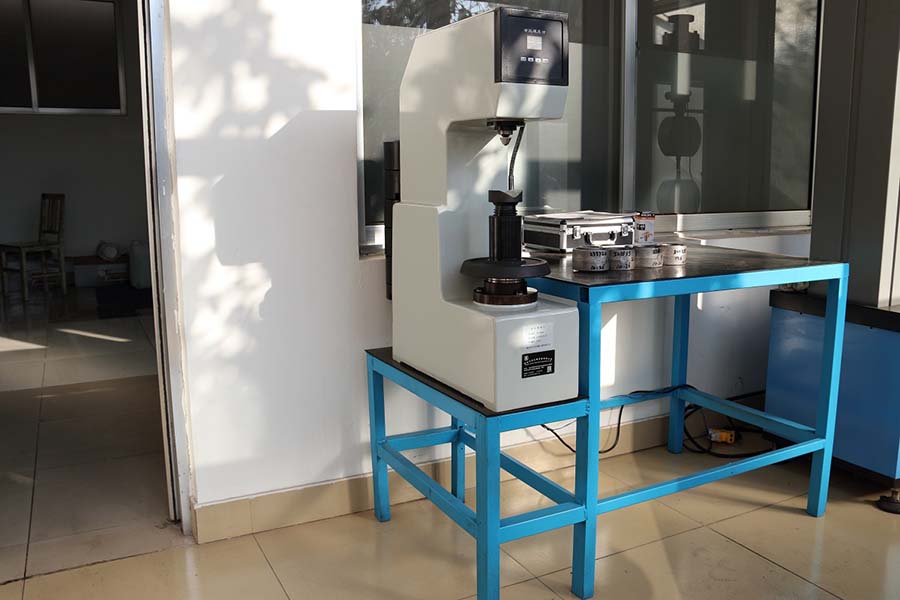
Hardness Tester
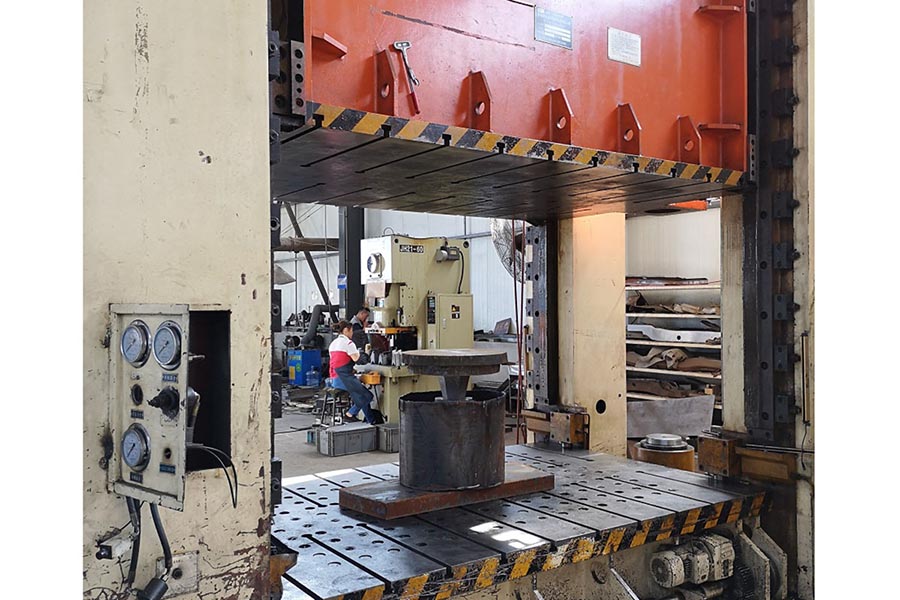
Press Testing for Mechanical Properties

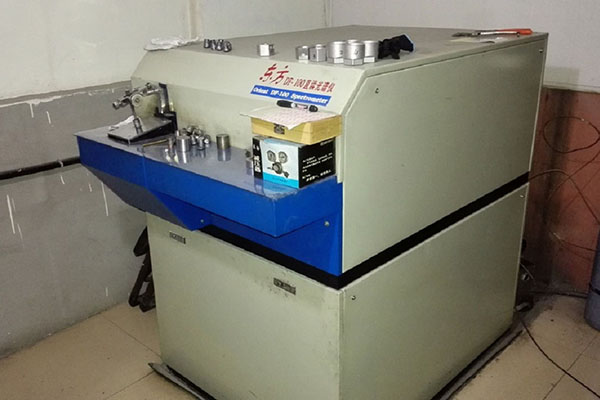
Spectrometer
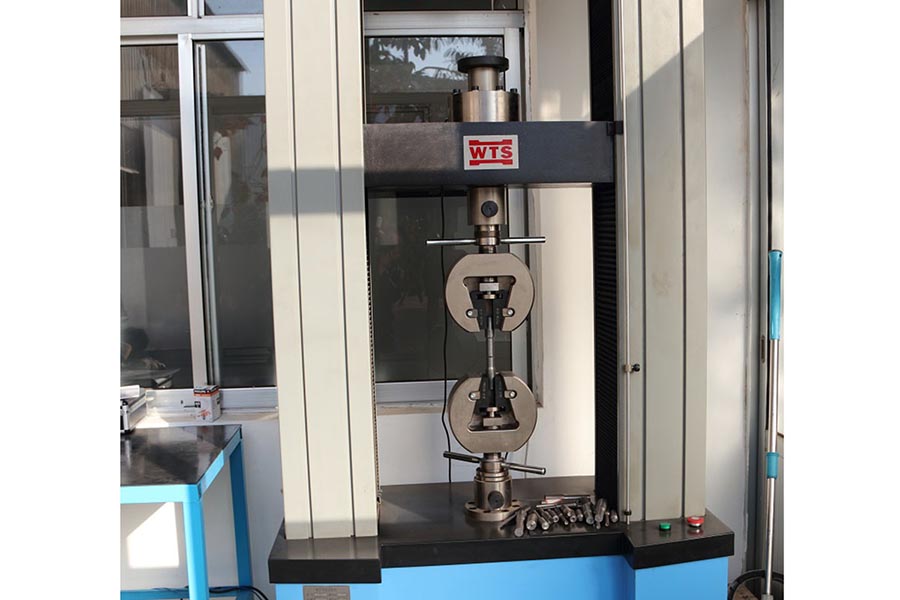
Tensile Tester
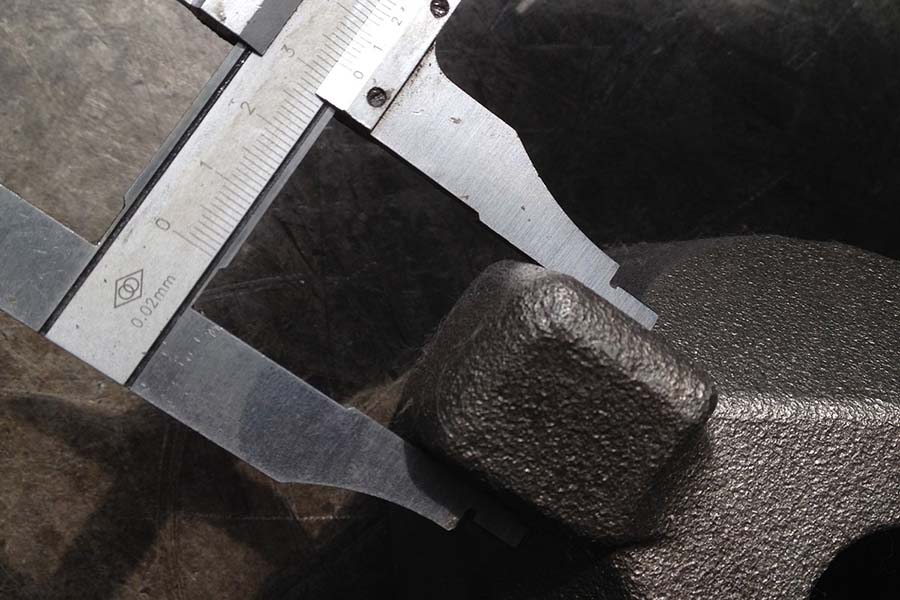
Vernier Caliper
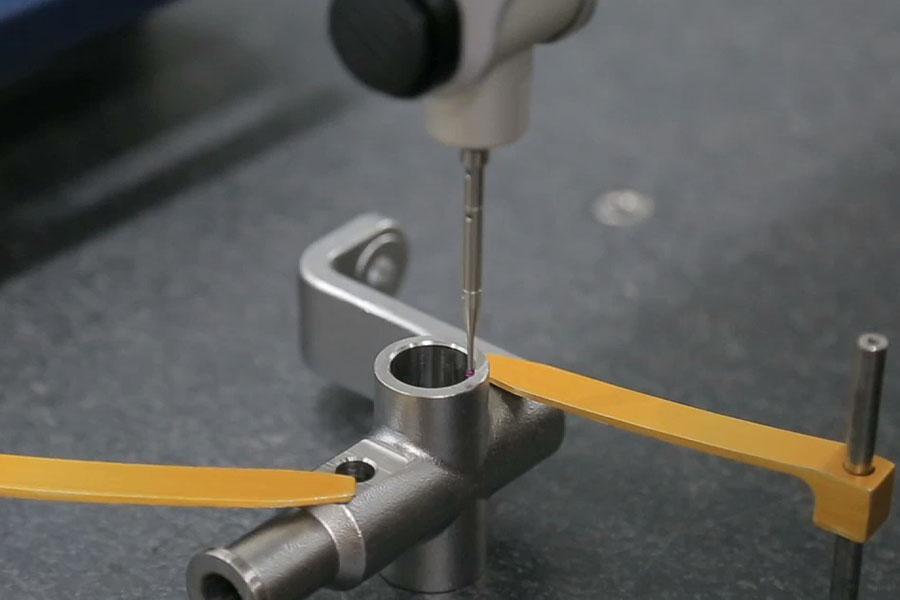
CMM

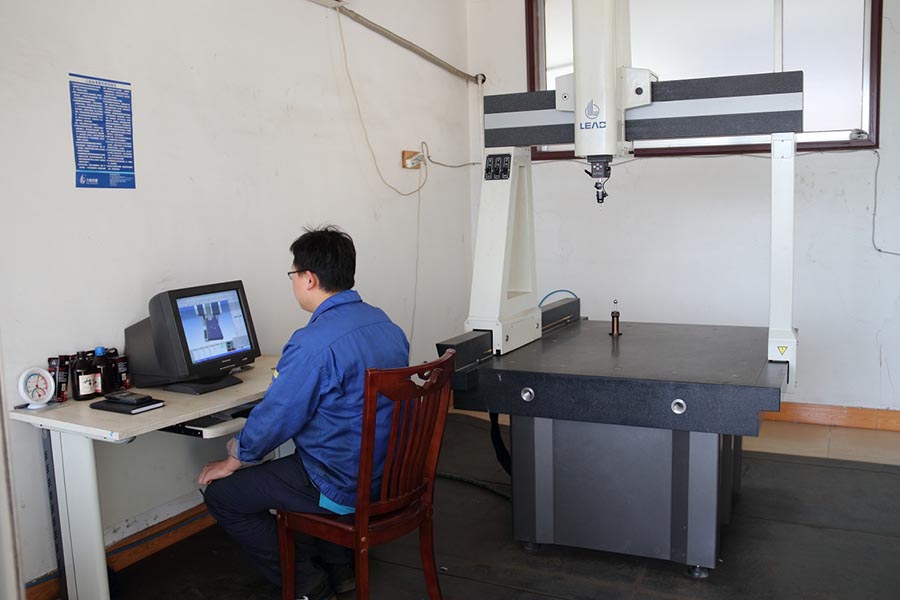
CMM
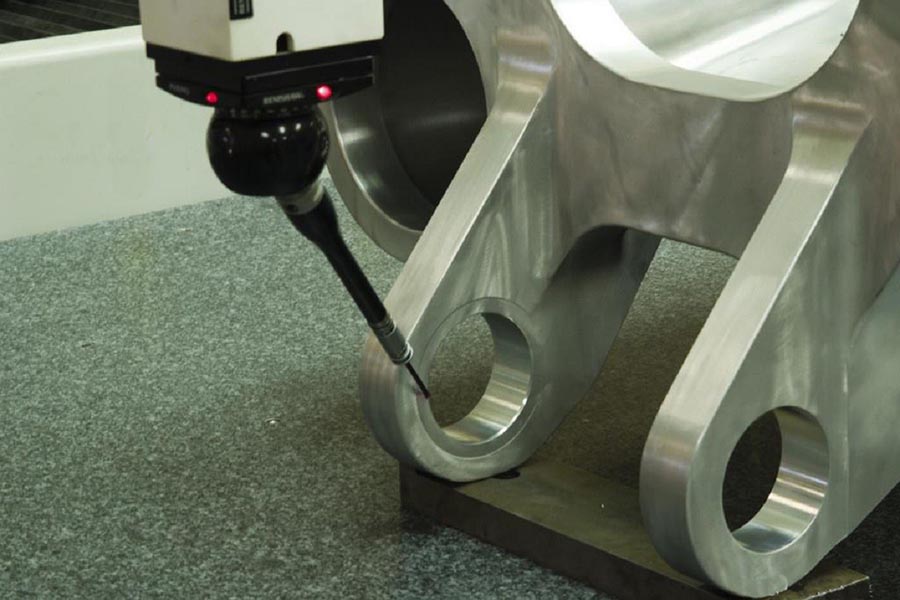
Dimensional Testing
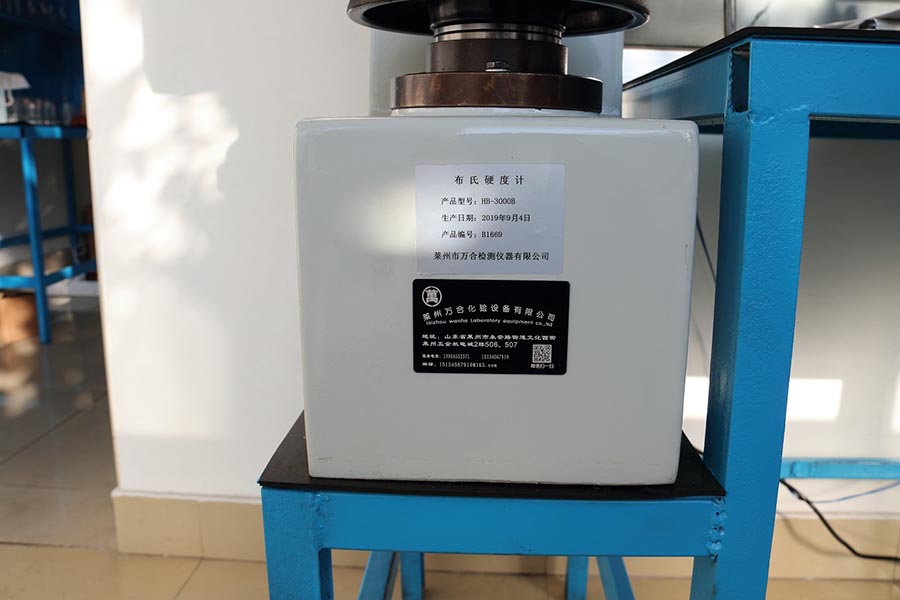
Hardness Tester

Dynamic Balancing Test
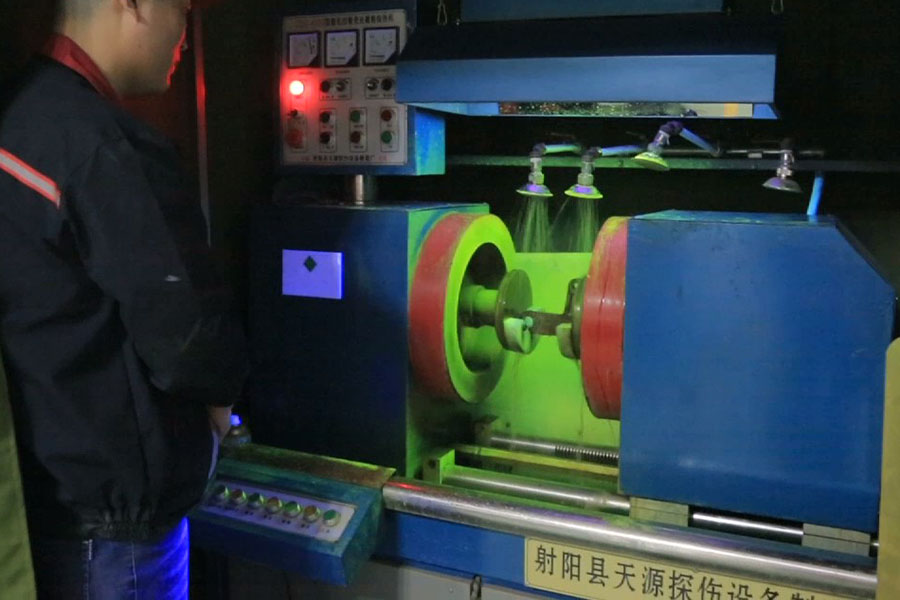
Magnetic Particle Testing
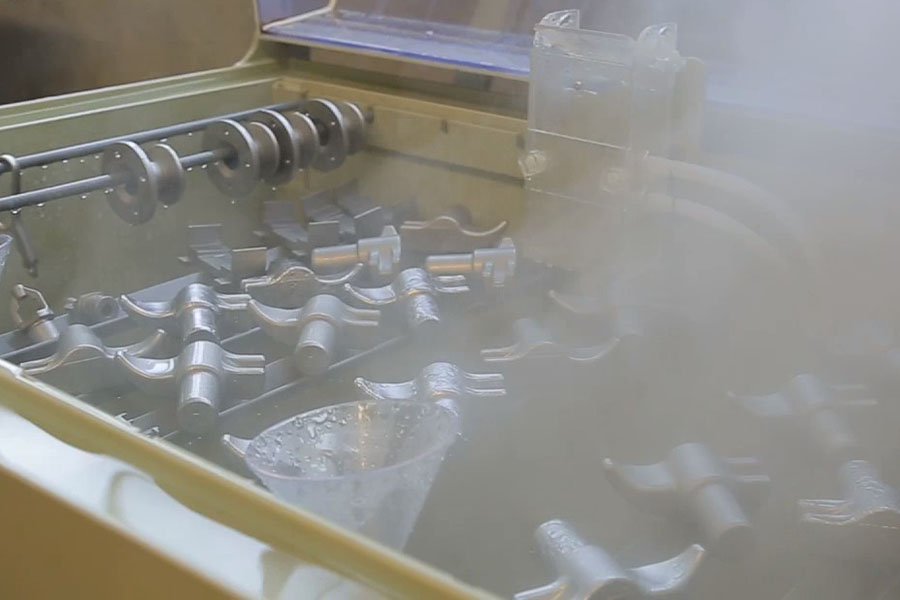
Salt and Spray Testing
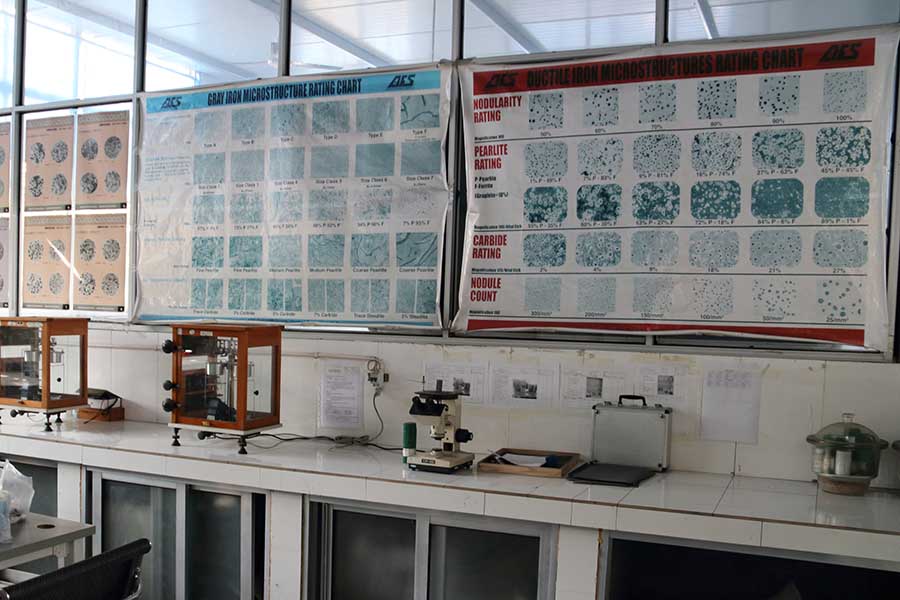